Article
Laying the groundwork for AI in supply chain management
Build a resilient supply chain with actionable AI-ready foundations
November 07, 2024
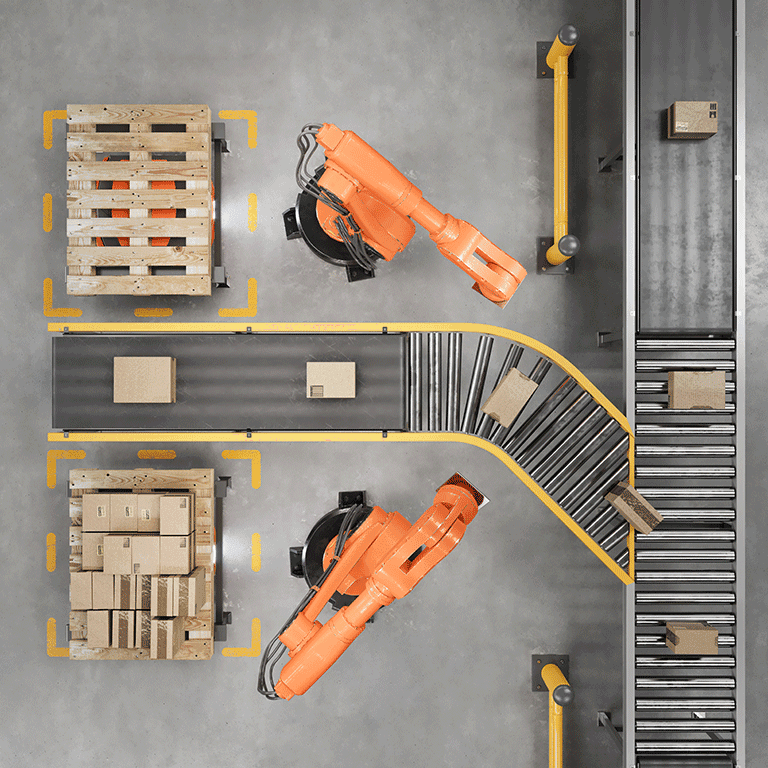
Pandemic-level supply chain disruptions continue to be a reality for many. According to the Manufacturing Leadership Council, 47% of companies report only minimal improvement in disruptions, with 4% still facing significant issues. Meanwhile, 23% now rate their supply chains as “not resilient”—a figure that nearly doubled in a year. Disruptions aren’t expected to ease any time soon.
Global political shifts, labor issues, and cyberattacks are reshaping supply chain management, calling for robust operational strategies. AI is increasingly part of that conversation, with 31% of manufacturers already using AI/ML for supply chain digitization and another 38% expecting to integrate it within two years.
AI has enormous potential to stabilize supply chains—but it’s not a cure-all. Effective AI deployment requires precise inputs, clean data, and strong foundational systems to support decision-making. Here’s how to assess and solidify the foundational areas essential to AI readiness:
1. Establish clear supply chain leadership to drive accountability
Start by consolidating supply chain responsibility within a dedicated executive role—ideally at the C-level—to ensure strategic focus on balancing growth, cost, and profitability. Elevating supply chain visibility to executive and board levels creates alignment on resilience as a strategic priority and allows for streamlined decision-making across functions. This change is essential, especially as companies increasingly recognize the supply chain’s critical impact on performance and strategic goals.
Many organizations still disperse supply chain responsibilities across departments, which can dilute focus and hinder responsiveness. Designating a C-level supply chain officer allows for coordinated oversight that integrates operations, sales, and marketing—meaning companies can act on a unified strategy that aligns with real-time market demands.
2. Implement integrated business planning across functions
Commit to a fully integrated business planning (IBP) approach that brings finance, operations, marketing, and technology to the table. Developing IBP starts with identifying key bottlenecks in supply chain processes, which might include common issues such as missed sales targets or stock shortages. Conduct root cause analysis to reveal underlying gaps, such as communication barriers between sales and operations, that hinder coordination.
A RACI (responsible, accountable, consulted, and informed) framework can strengthen IBP by clarifying roles and streamlining decision-making, reducing delays, and creating clearer accountability across departments. IT support is also crucial here, as digital integration is necessary to maintain accurate data flow and align forecasts with operational needs, making it possible to proactively adjust to demand shifts.
3. Prioritize data governance to build a solid data foundation
Focus on data governance to establish a clean, consistent data framework, allowing AI to function reliably. To manage rapidly growing data volumes, start by implementing data management protocols across systems, making sure data is accurate and accessible across departments. This foundation is essential for using AI effectively—poor data quality leads to misleading insights.
In addition, build data-sharing agreements with suppliers, logistics providers, and partners to streamline end-to-end visibility. Regular data access audits can identify and address gaps in accessibility, allowing you to control data flows and create a system that reliably supports AI-driven insights. Without these steps, attempts to deploy AI will likely be hindered by the time and cost of frequent data issues.
4. Optimize core supply chain systems before implementing AI
Before advancing to AI, ensure that foundational technologies like ERP, WMS, and TMS systems are fully optimized and effectively utilized. Audit how each system is currently used across functions, identifying areas where manual processes persist despite system capabilities. This close review often reveals critical gaps, like reliance on spreadsheets or manual data entry, which indicate that employees may not be fully leveraging available technology.
Maximizing these core systems enables a proactive approach to supply chain management by providing real-time visibility and data accuracy—both prerequisites for AI. By using technology to its full potential, your organization sets a solid baseline for the predictive and preventive capabilities that AI can deliver. Once these systems are in place, AI can then be layered in through existing platforms to drive targeted improvements in processes like anomaly detection, lead time prediction, and demand sensing.
Master the basics before scaling up
Prioritize foundational steps to prepare your supply chain for AI. Start with a thorough assessment of existing tools and processes to clarify where improvements are most needed, and then focus on addressing capability gaps in basic areas like data accessibility, technology alignment, and interdepartmental planning. Building momentum in these areas lays the groundwork for AI’s advanced potential, enabling an agile supply chain that turns disruption into a competitive advantage.