Article
Health Systems: Control your digital supply chain with a consolidated service center
COVID-19 has placed the spotlight on healthcare supply chains. Consolidated service centers offer a more efficient way forward.
October 29, 2020
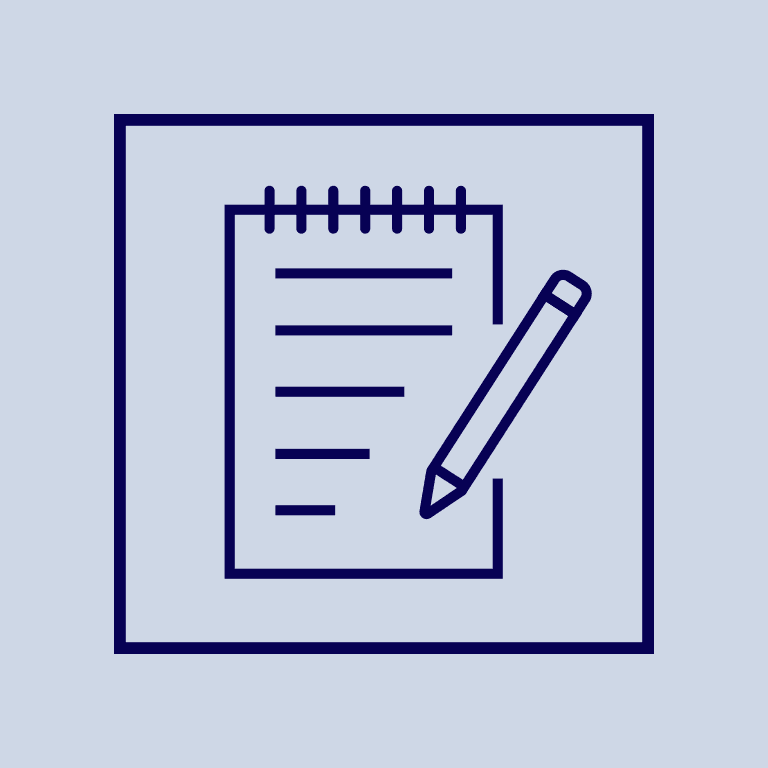
Shortages of personal protective equipment (PPE) and durable medical equipment (DME) have been a problem since the onset of COVID-19 in the United States and around the world. With so much dependence on various third parties for critical supplies as well as uncertainties around government intervention as the crisis unfolded, hospitals and health systems have found themselves in difficult positions as they strive to ensure they have the resources on hand to keep their patients and front line workers safe.
While questions remain about how this pandemic will play out and what measures will be put in place to mitigate the effects of future health crises, one thing seems certain: Healthcare providers need more control of and visibility into their supply chain processes. The just-in-time model has proven itself unfit for the task of dealing with a major public health disaster, and as insourcing/onshoring is becoming more prevalent, hospital and health system leadership have an opportunity to take control of their supply chains with a digitally-driven self-distribution model, move past fragmented systems and manual workarounds, and reduce reliance upon third parties.
This is where consolidated service centers (CSCs) come in. A CSC is a way to manage the sourcing, procurement, receipt, processing, packaging, shipment, distribution, and delivery of supplies—rather than relying solely on third-party service providers or distributors. Getting one set up for your hospital or health system is a way to control your own destiny, while realizing considerable cost savings.
Visibility and control: How a CSC works
CSCs allow healthcare organizations of all sizes to improve efficiency, margins, and clinical outcomes through supply chain digitization. Fundamentally, the idea is to move supplies from individual hospital storerooms to a central warehouse—the CSC—which services multiple hospitals, clinics, and associated practices.
With a CSC at the heart of your self-distribution model, clinicians can easily check the availability of items across their networks and know with confidence that supplies will be delivered when needed. Additionally, CSCs minimize the opportunity for individual floors, departments, clinics, and storerooms to hoard supplies and cause imbalances elsewhere in your organization. The self-distribution approach also means pickup and replacement require minimal effort by personnel at each facility.
A CSC provides the visibility healthcare organizations need to right-size their inventory, while process standardization helps improve the quality and consistency of care, reduce patient risk and cost while increasing efficiency.
Additional benefits include collaboration and empowerment
A CSC fosters collaboration across a health system network and it improves flexibility. A self-managed model empowers your organization in ways that aren’t possible when sourcing is completely dependent on distributors, wholesalers, and other third parties. Having better visibility on inventory and usage across your network puts you in position for strategic sourcing—buying in bulk or negotiating better rates based on overall volume, for example—which can reduce overall spend.
Additionally, taking control of your supply chain with a CSC will drive down logistics and handling costs while allowing providers to focus on care delivery without worrying about whether or not they have the supplies they need. This way, your organization has the supply chain resiliency to respond and recover to all types of challenging situations.
Getting started: Digital supply chain optimization with a CSC
More than 70 health systems of various sizes across the United States are using CSCs – and top performers have reduced supply chain expenditures by up to 65%, a significant number considering that supply chain costs are among the biggest drags on a hospital’s or health system’s bottom line. Even small health systems have successfully implemented CSCs, affording themselves the flexibility to expand their operations and opening a platform for business growth. So how do you get started?
The good news is establishing a CSC isn’t that difficult—pop-up CSCs can be set up in as little as four weeks—but there are four keys to getting it right:
- Attain organizational alignment: When you start the process, know what you want to accomplish and clarify your value proposition. Like with any transformation, the result will only be as good as your plan and the buy-in you gain across your organization.
- Determine the operating model to fit your needs: You might consider anything from a 100% outsourced model to 100% insourced. Wherever you land, it’s important to select a platform that can support an expanded capacity upfront to allow room for growth.
- Partner on platform selection and change management: A strong change management partner will work with you to evaluate your situation, identify the time and best practices required to achieve your goals, and help you identify and implement the best technology solution for your needs.
- Rely on your partner: Your change management and implementation partner will reduce the burden of oversight by handling the challenges of getting you started and providing oversight for the duration of your project, monitoring and tracking implementation progress and keeping the rollout of your CSC on track.
Seize the opportunity and take control
Many healthcare organizations fall short of their goals on cost, quality, and outcomes because they lack control of their own supply chain. This dependence also creates vulnerabilities to disruption—the current pandemic has highlighted the need for consolidated, streamlined supply chain management as organizations have struggled without the appropriate processes and technologies in place to identify shortages well enough in advance. Other needs include procuring, tracking, storing, and ultimately distributing supplies to their departments and front-line staff in a timely and efficient manner—all of which can be achieved through the digitization of the supply chain process.
Given the turmoil of the past several months, it might still be tempting to stay the course and continue relying on third parties in a just-in-time model. But that would be a missed opportunity. Instead, improve your digital supply chain management with a self-distribution model organized around a CSC. Taking this step will allow you to focus on efficiency, control, and disaster planning as you move past external dependencies, fragmented systems, and manual workarounds. A CSC generally pays for itself in less than two years.
Contact us to learn more about how a CSC works and how we can help you quickly identify and establish the right solution for your organization’s needs.